新聞中心
汽車輕量化勢不可擋,一體化壓鑄積極布局
發(fā)布時間:
2024-09-30 13:11
來源:
機動車成為重要大氣污染源,碳減排目標下汽車低碳化發(fā)展刻不容緩。根據 中國政府網發(fā)布的《第二次全國污染源普查公報》,2017 年全國大氣氮氧化物排 放量 1785.22 萬噸,顆粒物排放量 1684.05 萬噸,揮發(fā)性有機物排放量 1017.45 萬噸。2017 年統(tǒng)計匯總機動車保有量 2.67 億輛,其排放氮氧化物 595.14 萬噸、 顆粒物 9.58 萬噸、揮發(fā)性有機物 196.28 萬噸,分別占全國比重為 0.57%、33.34%、 19.29%。對此,《節(jié)能與新能源汽車技術路線圖 2.0》提出,我國汽車技術發(fā)展的 總體目標之一為汽車產業(yè)碳排放總量先于國家碳減排承諾于 2028 年左右提前達 到峰值,到 2035 年排放總量較峰值下降 20%以上,汽車減排、低碳化發(fā)展迫在 眉睫。
汽車輕 量化就是在保證汽車的強度和安全性能的前提下,盡可能地降低汽車的整備質量, 從而提高汽車的動力性,減少燃料消耗,降低排氣污染。世界鋁業(yè)協(xié)會的報告指 出,汽車整車重量降低 10%,燃油效率可提高 6%-8%。大眾汽車研究認為,汽車 整備重量每減少 100 千克,每公里二氧化碳排放可減少 8-11g,百公里油耗可降 低 0.3-0.5 升。因此,在當前汽車減排壓力日益增大的背景下,汽車輕量化對于節(jié) 約能源、減少排放、實現可持續(xù)發(fā)展戰(zhàn)略具有十分積極的意義。
1.1. 燃油車減耗目標高,整車減重可有效提升燃油效率輕量化成為燃油車發(fā)展重點方向,2025 年燃油乘用車整車輕量化系數降幅目 標為 10%。在燃油車減耗目標下,大力發(fā)展汽車輕量化技術、持續(xù)構建汽車輕量 化技術開發(fā)和應用體系變得至關重要。《節(jié)能與新能源汽車技術路線圖 2.0》摒棄 以整車裝備質量和輕質材料用量為衡量標準的傳統(tǒng)做法,引入整車輕量化系數等 作為衡量整車輕量化水平的依據,并提出 2025 年、2030 年、2035 年我國燃油乘 用車整車輕量化系數需分別降低 10%、18%、25%,載貨車、牽引車和客車分別 降低 5%、10%、15%。
1.2. 電動車三電系統(tǒng)重量大,提升續(xù)航里程需求推動輕量化發(fā)展2022 年新能源汽車滲透率同比快速提升,全國新能源汽車保有量大幅增長至 1310 萬輛。據公安部統(tǒng)計,2022 年全國新能源汽車保有量達 1310 萬輛,占汽車 總量的 4.10%,扣除報廢注銷量比 2021 年增加 526 萬輛,增長 67.13%。其中, 純電動汽車保有量 1045 萬輛,占新能源汽車總量的 79.78%。2022 年全國新注 冊登記新能源汽車 535 萬輛,占新注冊登記汽車總量的 23.05%,與上年相比增 加 240 萬輛,增長 81.48%。新注冊登記新能源汽車數量從 2018 年的 107 萬輛 到 2022 年的 535 萬輛,呈高速增長態(tài)勢。
與燃油車相比,新能源汽車減重需求更為迫切: 1)新能源車整車質量高于傳統(tǒng)燃油車。與燃油車配備發(fā)動機、變速箱不同, 新能源汽車動力來源于電池、電驅、以及電控三大系統(tǒng),合計占整車質量的 30- 40%。在現有電池密度水平下,新能源汽車的動力系統(tǒng)質量顯著高于燃油車。尤 其是圍著網聯化、智能化不斷推進,未來搭載相關配置后,整車質量將進一步提 升。 2)新能源汽車續(xù)航里程為用戶核心關切,降低整車質量提升續(xù)航能力將進一 步增強新能源汽車競爭力。一般而言,新能源汽車續(xù)航里程取決于電池容量、電 機效率、溫度、工況等多種因素影響。盡管當前新推出車型續(xù)航里程有所增加,然 而實際行駛續(xù)航里程往往與官方公布的有較大差距,甚至在冬季出現續(xù)航減半的現象,這嚴重影響了消費者的購買決策。而國家新能源汽車技術創(chuàng)新中心研究表 明,降低整車質量能顯著提升續(xù)航里程,整車重量每降低 10kg,續(xù)航里程可增加 約 2.5km。 因此,中國汽車工程學會提出到 2025 年、2030 年、2035 年純電動乘用車輕 量化系數分別降低 15%、25%、35%。
2. 材料、結構、工藝輕量化為汽車減重三大著手點為滿足汽車輕量化壓鑄的技術需求,目前行業(yè)內主要在材料、結構設計、工 藝三方面進行突破,根據產業(yè)前沿技術:
1)材料輕量化:選用結構強度有保障的、密度相對低的材料代替?zhèn)鹘y(tǒng)的鋼材 料,包括高強度鋼、鋁合金、鎂合金、碳纖維等材料。從而通過降低材料密度和用 量實現整車減重。從減重效果來看,碳纖維最好;從成本來看,高強度鋼較低。
2)結構輕量化。在不影響車身基本狀態(tài)的情況下,通過采用先進的優(yōu)化設計 方法和技術手段,優(yōu)化車身結構參數,去除零部件冗余部分的同時實現壁化、中 空化、小型化、復合化,從而提高材料利用率。通過合理的結構設計減少材料用量 實現輕量化。根據設計變量及優(yōu)化問題類型的不同,結構輕量化可分為拓撲優(yōu)化、 尺寸優(yōu)化、形狀優(yōu)化、形貌優(yōu)化四種。一般而言,采用新材料和新工藝會使得開發(fā) 成本大幅增加,而結構優(yōu)化由于未采用新的材料,實現減重的同時能降低成本, 是車身輕量化最常用的方法之一。
3)工藝輕量化。激光拼焊技術是汽車廠商最常用的方法,其原理是采用不等 厚度軋制板,通過計算機實時控制和調整軋輥的間距,以獲得沿軋制方向上按預 先定制的厚度連續(xù)變化的板料。此外還有液壓成形、熱成形;輥壓成形技術;低 (差)壓鑄造成型技術以及各種汽車輕量化連接技術等。值得一提的是,特斯拉 推出的一體化壓鑄技術則在制造工藝端和材料端引領革新。
2.1. 材料輕量化:高強度鋼為當前主流,鋁合金增量可期在三大輕量化手段中,材料輕量化是基礎。在采用輕量化材料的基礎上,通 過優(yōu)化結構、升級工藝等方式,實現整車減重。因此在輕量化材料發(fā)展方面,《節(jié) 能與新能源汽車技術路線圖 2.0》指出,我國自主輕量化技術開發(fā)和應用體系的構 建,近期以完善高強度鋼應用為體系重點,中期以形成輕質合金應用體系為方向, 遠期形成多材料混合應用體系為目標。
2.1.1. 高強度鋼:屈服強度和抗拉強度高,當前應用最為廣泛高強度鋼板屈服強度、抗拉強度高。按照國際鋼鐵協(xié)會 USL-AB 項目,可將 鋼種按其力學性能進行分類,分為低強鋼(軟鋼)、高強鋼以及超高強鋼。低強鋼 的抗拉強度 Rm(σb)<270MPa,屈服強度 Re(σs)<210MPa;超高強鋼的 抗拉強度 Rm(σb)>700MPa,屈服強度 Re(σs)>550MPa;高強鋼的力學 指標介于這兩者之間。其中,低強度鋼分為 IF 鋼和軟鋼;普通高強度鋼分為碳錳 鋼、BH 鋼、高強度 IF 鋼和 HSLA 鋼等;先進高強度鋼(AHSS)包括雙相鋼(DP 鋼)、相變誘發(fā)塑性鋼(TRIP 鋼)、復相鋼(CP 鋼)和馬氏體鋼(MS 鋼)等。
整車中鋼材用量大,占整車自重 55-60%。據汽車材料網,以現代轎車用材為例,按照重量換算,鋼材占汽車自重的 55%-60%,鑄鐵占 5%-12%,有色金屬占 6%-10%,塑料占 8%-12%,橡膠占 4%,玻璃占 3%,其他材料(油漆、各種液 體等)占 6%-12%??梢婁摬脑谄囍杏昧枯^大,高強度鋼板的應用能減輕沖壓件的重量,節(jié)省能源和降低沖壓產品成本。用于汽車零件的高強度鋼板,其抗拉 強度可以達到600-800MPa,而相應的普通冷軋軟鋼板的抗拉強度只有300MPa。 目前,全球最大的鋼鐵公司 Acelor 開發(fā)了熱沖壓成形鋼板 USIBOR1500。該鋼板 為鍍鋅板,鍍層質量為 120-160g/m2,淬火后力學特性明顯,強度值可達到 1600MPa。
根據 AEE 汽車技術平臺,高強度鋼可以應用于汽車面板、車體框架以及底盤 等多個部位:
1)汽車面板:車頂、車門等部件要求具有變形剛度和抗凹陷性,主要使用抗 拉強度為 340-390MPa 的烘烤硬化鋼板(BH 鋼板)。BH 鋼板的屈服強度在烘烤 涂漆時升高,可在不損失成形性的前提下,提高抗凹陷性,減薄鋼板?,F在有的車 型已使用 440MPa 級 BH 型高強度鋼板。新馬自達 2 的車身結構中就使用了 440、 590、780 和 980Mpa 級別的高強度鋼板和超高強度鋼板。
2)車體框架:隨著正面撞擊、側面撞擊的撞擊安全性標準的提高,結構件、 加強件等主要使用 590MPa 級高強度鋼板,也有廠家使用 780MPa 級、980MPa 級高強度鋼板。有些廠家甚至采用將 390MPa、440MPa 級高強度鋼板沖壓成形 后,對強化部分進行高頻加熱和淬火,以使部件局部抗拉強度達到 1200MPa,并 在沖壓加熱鋼板的同時進行冷卻,以使部件整體抗拉強度達到 1470MPa 的方法。 此外,還有采用激光拼焊方法,將不同厚度、不同材質鋼板拼合起來,使材料配置 適用于所要求材質和使用部位。
3)汽車底盤:汽車底盤的用材已從傳統(tǒng)的 440MPa 級熱軋板發(fā)展到 780MPa, 最大減重達 30%。近年來,高強度鋼板在底盤上的使用比例正在急劇增加。今后, 高強度鋼板的使用比例及更高強度鋼板的應用有望進一步提高。
多個項目證實高強度鋼能在不增加成本的條件下實現輕量化。根據《軋鋼》 雜志,為了推進高強度鋼在汽車上的應用,國際鋼鐵協(xié)會組織開展了多個項目, 包括超輕鋼制車(ULSAB)、先進概念車超輕鋼制車身計劃(ULSAB-AVC)、未來 鋼制汽車(FSV)等。
1)ULSAB 項目:主要目標是減小車身質量、提高結構強度、提高安全性、 簡化制造工藝及降低生產成本。ULSAB 車身重量 203kg,與對標車相比減重 25%, 高強度鋼應用比例 91%。冷沖壓成形應用比例 42.8%,激光拼焊板應用比例 44.9%, 液壓成形比例 9.3%。 2)ULSAB-AVC 項目:通過車輛的整體設計來實現車身的輕量化,高強度鋼 的應用比例達到 97%。在成形技術方面,有 30%以上的零件采用激光拼焊板,20% 以上的零件采用液壓成形技術。 3)FSV 項目:表明先進高強度鋼能夠達到碰撞安全五星評價的要求,并降低 車輛在整個使用周期內的總排放量,在不增加成本的條件下實現輕量化。
2.1.2. 鋁合金:減重性價比高,中長期增量可觀鋁合金減重效果、提升汽車性能、循環(huán)利用等優(yōu)勢顯著。鋁合金是地殼中含 量最為豐富的綠色金屬,與其他材料相比,鋁件不但輕、比強度高,而且易于成 形,吸能效果好,耐腐蝕,循環(huán)利用價值大。此外,鋁合金在減重的同時,能實現 汽車更好的剎車性、更優(yōu)的操控性、更好的駕駛舒適度和更突出的動力。根據汽 車材料網,其具體優(yōu)勢優(yōu)勢在于:
1)減重、節(jié)能減排效果好。 ①減重效果。根據美國鋁業(yè)學會的報告,汽車中每使用 1kg 鋁,可以獲得 2.2kg 的減重效果,且服役期內將減少 20kg 尾氣排放。鋁合金由于密度較鋼材小,用在 汽車零部件上能夠實現二次輕量化。據美國鋁業(yè)公司的研究,汽車典型零件用鋁 的一次輕量化效果可達 30%-40%(以高強度鋼代替普通鋼材能減重約 11%),二 次輕量化效果可提高至 50%。 ②減排效果。汽車的油耗一定程度上與整車質量相關,一般而言,整車質量 越大,汽車油耗越高。而二氧化碳排放量又與油耗呈正相關。因此通過降低整車 質量,能夠減少汽車油耗,從而使得二氧化碳排放量減少。
2)提高行駛性能、安全性能、舒適性及穩(wěn)定性。 ①行駛性能。由于使用鋁合金能夠減輕汽車質量,從而能夠減少百公里加速 時間,提升行駛性能。據美國鋁業(yè)協(xié)會研究,若鋁合金在汽車中實現 25%的輕量 化效果,那么汽車加速到 96.56km/h 的時間就能夠縮短 4s。 ②安全性能。在同樣設計要求條件下,鋁合金吸收碰撞的性能比鋼材優(yōu)異。 因此當汽車發(fā)生碰撞時,與鋼材相比,鋁合金材料更容易形成褶皺和變形,會多 吸收 50%-70%的沖擊力,從而提高汽車安全性。 ③舒適性及穩(wěn)定性。鋁合金在汽車上使用通常會使得汽車整體重心降低,汽 車駕駛的舒適性及穩(wěn)定性相應得到提高。
3)裝配效率高、易回收。鋁合金整體車身需要點焊的部分較少,加工工序縮 短,且其不易生銹,不需要做防銹處理,可顯著提高汽車裝配效率。此外,由于鋁 合金熔點較低,在使用期間腐蝕率低且程度輕微,因此便于回收利用。
4)成本較碳纖維低、原材料自供率高。鋁合金價格僅高于高強度鋼,遠低于 碳纖維復合材料。而鎂合金由于自身化學特性,耐腐蝕性不及鋁合金,這一定程 度上限制了其在汽車領域的大規(guī)模應用。因此綜合而言,現階段鋁合金是理想的 汽車輕量化材料。此外,我國氧化鋁、電解鋁產量均為世界第一,原材料自供率 高。
鋁合金為輕量化最優(yōu)材料之一,中長期增量可觀。與高強度鋼相比,鋁合金 由于密度低,減重效果更明顯,且不存在鎂合金易腐蝕、加工成本高昂以及碳纖 維原材料價格高、回收利用較為困難等問題。此外,鋁合金優(yōu)良的金屬性質使其 可以更好地結合結構、工藝輕量化,達到綜合減重的目的?!豆?jié)能與新能源汽車技 術路線圖》中規(guī)劃了我國輕量化分階段目標,2025 年與 2030 年單車鋁合金將分別達到 250kg、350kg,用量將大幅超越高強度鋼。未來隨著輕量化趨勢不斷加深, 輕量化材料、技術不斷提升,鋁合金將成為汽車市場主要的材料,長期增量優(yōu)勢 明顯。
2.1.3. 工程塑料:由內外飾件延伸至功能結構件,發(fā)展前景廣闊塑料種類繁多,是汽車輕量化的重要材料。隨著汽車節(jié)能減排、新能源汽車 的興起,汽車輕量化成為行業(yè)主流,塑料在汽車上的應用也越來越多。根據各種 塑料不同的使用特性,通常將塑料分為通用塑料、工程塑料和特種塑料三種類型。 工程塑料用于汽車的主要作用是使汽車輕量化,從而達到節(jié)油高速的目的。發(fā)達 國家將汽車用塑料量作為衡量汽車設計和制造水平高低的一個重要標志,世界上 汽車塑料單用量最大的是德國,塑料用量占整體材料的 15%。據汽車工藝師,新 能源汽車高壓電氣部分,在性能滿足要求的情況下將部分金屬更換為塑料可以減 重 30%左右。目前一輛純電動車采用塑膠輕量化可減重 100KG 左右,實現節(jié)能 減排。工程塑料在汽車領域的應用已從汽車用內外飾零部件延伸至結構性及功能性 部件。根據汽車材料網,車用塑料有很多以往傳統(tǒng)材料沒有的優(yōu)點,主要表現在 重量輕、有良好的外觀裝飾效果、有多種實際應用功能、有良好的理化性能、容易 加工成型、節(jié)約能源,可持續(xù)利用等各方面。1)在汽車外裝件上的應用是為了以 塑代鋼,減輕汽車自重。主要應用包括:保險杠、擋泥板、車輪罩、散熱器格柵、 擾流板等。2)在汽車內裝件上的應用是為了安全、環(huán)保和舒適。主要應用包括: 儀表板、車門內板、副儀表板、雜物箱、座椅后護板等。3)結構件和功能件主要 采用高強度的工程塑料,主要應用包括:油箱、散熱器水室、空濾器殼體、風扇葉 片等。
2.1.4. 碳纖維:減重幅度最大,成本高+回收利用困難制約發(fā)展日美碳纖維發(fā)展處于領先地位,中國正加快發(fā)展步伐,2021 年碳纖維國產化 率水平已達 47%。我國碳纖維行業(yè)起步于 20 世紀 60 年代,幾乎和日美等國家同 時起步,但由于相關知識儲備不足、知識產權歸屬等問題,發(fā)展緩慢。同時,日本、美國等國家對碳纖維核心技術形成壟斷,我國碳纖維生產技術和裝備水平整 體落后于國外。2000 年以來,國家加大對于碳纖維領域自主創(chuàng)新的支持力度,將 碳纖維列為重點研發(fā)項目。伴隨著國家政策的大力扶持,國內碳纖維行業(yè)在技術 上取得重大突破,產業(yè)化程度快速提升,應用領域不斷擴大,地區(qū)上目前已形成 以江蘇、山東和吉林等地為主的碳纖維聚集地。國內主要企業(yè)有吉林化纖、中復 神鷹、中材科技、光威復材等。據前瞻產業(yè)研究院,2021 年中國大陸地區(qū)碳纖維 產能首次超過美國成為全球最大產能國,產能達到 6.34 萬噸,占全球總產能比重 超過 30%,產量達到 2.43 萬噸,同比增長 30.03%。
材料成本、加工工藝及材料回收再利用問題制約碳纖維在汽車領域的應用。 根據汽車輕量化技術創(chuàng)新戰(zhàn)略聯盟,當前阻礙碳纖維材料在新能源汽車領域中得 到大范圍普及運用的關鍵在于: 1)材料成本高昂。碳纖維材料與傳統(tǒng)的鋼材料及鋁合金相比較,其實際加工 更為昂貴,部分汽車采用碳纖維材料后,僅車身的材料成本價就高達上萬元,部 分采用優(yōu)質碳纖維材料的汽車車身甚至超過 2 萬元。 2)加工工藝局限使得碳纖維制品抗穿刺性能差。相對于傳統(tǒng)材料來說,碳纖 維材料抗剪斷能力較弱,因此在具體應用過程中必須要進行重疊成型,以此來保 障應用后的質量及效果。此種生產工藝促使碳纖維材料具有良好的抗沖擊性能, 但實際抗穿刺性能卻較差,在受力過大的情況下將會出現構件斷裂等問題,并且 此問題在出現后無法進行修復,僅能夠更換處理。 3)材料回收再利用。CFRP 不能自然降解,焚燒或填埋是早期通行的處理方 法,但 CFRP 廢棄物焚燒會產生大量有毒、有害氣體,影響自然環(huán)境,同時填埋 焚燒后的廢渣也會造成土壤二次污染;而填埋法處理 CFRP 廢棄物在污染土壤同 時會占用大量土地資源。目前主要回收方法有機械回收法、熱回收法及溶劑回收 法等,但國內 CFRP 回收尚未形成規(guī)?;?、產業(yè)化。
2.1.5. 鎂合金:減重效果僅次于碳纖維,腐蝕問題和制造工藝難題有待突破鎂合金性能優(yōu)點顯著,用于汽車殼體、支架、扶手結構以及汽車顯示系統(tǒng)等 多領域。鎂合金作為最輕的金屬材料,具有密度低、強度高、散熱性能好、抗震減 噪性能優(yōu)等特征。壓鑄鎂合金的密度僅為鋁合金的 2/3,鋼鐵的 1/4,比強度和比 剛度均優(yōu)于鋼和鋁合金,遠高于工程塑料。由于其特性優(yōu)良,可用于汽車殼體、支 架、扶手結構以及汽車顯示系統(tǒng)等多領域,目前市場客戶群體對于車燈散熱支架、 儀表盤支架、轉向支架、中控骨架以及車載顯示屏框架等車身部件關注度相對較 高,接受程度較好。
據 AEE 汽車技術平臺,鎂合金材料的成形方法分為鑄造加工成形和塑性成 形,制造工藝同樣制約了鎂在汽車領域的廣泛應用。 1)鑄造成形。當前主要運用方法,且壓鑄方法是鎂合金鑄造成形方法中應用 最廣泛的。最近發(fā)展起來的鎂合金壓鑄新技術包括充氧壓鑄和真空壓鑄,充氧壓 鑄在生產汽車鎂合金零部件上的應用較廣泛,真空壓鑄可生產出 AM60B 鎂合金 汽車方向盤和輪轂。鎂合金成形以鑄造工藝為主,但鑄件的缺陷限制了鎂合金性 能的提高,局限了鎂合金的廣泛應用。 2)塑性成形。鎂合金使用塑性成形方法,可有效地消減鑄件缺陷的影響,通 常采用熱處理強化和形變強化可明顯地提高合金的性能,但由于鎂的密排六方結 構,變形難度比鋼、鋁和銅等要大。如果直接運用鋁合金已有的塑性成形方法,往 往會使得鎂合金材料的成品率很低,使塑性加工成形成本過高,影響了鎂合金在 各領域的應用。因此,加快發(fā)展鎂合金塑性成形方法也是研究的熱點和發(fā)展的趨 勢。
2.2. 結構輕量化:幾種方式各具優(yōu)勢,拓撲優(yōu)化為事前優(yōu)化極具應用價值據《汽車結構輕量化的研究與進展》,結構輕量化是指通過參數優(yōu)化(尺寸、 形狀、位置和厚度等)、形貌優(yōu)化、拓撲優(yōu)化等方式對零件進行開發(fā)和設計,在 剛度、強度保持不變或增加的基礎上,改變零部件的形狀和形式,以減少重量。
1)尺寸優(yōu)化:發(fā)展最早,也是最為成熟的一種汽車結構輕量化技術。尺寸優(yōu) 化的原理是在結構的類型、材料、外形以及布局給定的情況下,以滿足典型工況 下的剛度、強度和模態(tài)為約束條件,以汽車結構質量最小作為目標函數,將部件 的尺寸作為設計變量,來搭建優(yōu)化數學模型的一種優(yōu)化方法。王繼峰《參數優(yōu)化 技術在汽車車架輕量化中的應用》一文中以車架厚度為自變量,對重型汽車車架 進行了結構輕量化設計,經過優(yōu)化后,車架部分梁厚度減小,車架總質量由 691kg 降低到 654kg,減輕了 5.4%輕量化效果顯著。
2)形狀優(yōu)化:不改變現有拓撲模式下,以零部件的幾何外形作為設計變量進 行優(yōu)化,結構受力更均勻,材料利用更充分。形狀優(yōu)化的主要原理是在汽車結構 的類型、布局和材料給定的情況下,對結構的幾何外形進行改變,使得結構受力 更加均勻,材料利用更加充分,從而達到汽車結構輕量化。一般而言,形狀優(yōu)化 主要分為有參形狀優(yōu)化(對于形狀規(guī)則的結構,將結構的幾何外形進行參數化, 然后對參數進行優(yōu)化)和無參形狀優(yōu)化(對于形狀不規(guī)則的結構,以形狀變量為 設計變量,對結構進行形狀優(yōu)化)。
3)形貌優(yōu)化:能在減輕結構質量的同時能滿足強度、頻率等要求,尤其適合 用于板殼結構。形貌優(yōu)化的原理是以加強筋、凹凸結構的形狀、位置和數量等為 變量,在不顯著增加質量的條件下,以形狀為變量改善鈑金結構件的剛度及模態(tài) 等。形貌優(yōu)化由于不刪除材料,能在減輕結構質量的同時能滿足強度、頻率等要 求,可以靈活設定平面起筋的類型,包括高度,寬度和角度,從而滿足工藝要求, 尤其適合用于板殼結構。
4)拓撲優(yōu)化:在結構布局尚未確定的情況下進行優(yōu)化設計,極具應用價值。 與尺寸優(yōu)化和形狀優(yōu)化不同,而拓撲優(yōu)化是在概念設計階段,在布局尚未確定的 情況下進行優(yōu)化設計,是有限元分析和數學優(yōu)化方法的有機結合。其原理是是在 指定的設計空間內,在滿足約束條件和設計目標的前提下,在一個給定的空間區(qū) 域內,依據已知的外載及支承等約束條件,尋找承受單載荷或多載荷物體的最佳 結構材料分配方案,從而使結構的剛度達到最大或使輸出位移、應力等均達到規(guī) 定要求的一種結構設計方法。其優(yōu)點在于可以避免設計的盲目,提高結構設計的 效率,用較少的材料生產出合格的產品,達到結構輕量化等工程目的。
2.3. 工藝輕量化:多種輕量化工藝協(xié)同發(fā)展,熱成形過去十年應用廣泛輕量化工藝作為汽車輕量化的三大途徑之一,可以從制造層面有效地幫助汽 車達到節(jié)能減重的效果。汽車輕量化技術追求在保證汽車使用性能、安全性和性 價比的前提下,將輕量化結構設計與多種輕量化材料、輕量化工藝技術集成應用, 降低汽車的整車質量,從而減少燃料消耗,提高汽車動力,減輕排放污染。工藝輕 量化以汽車整體輕量化設計為基礎,綜合考慮所采用輕量化材料的特性、輕量化 結構設計的要求和產品成本控制而采用的制造技術。
1)激光拼焊:可實現不同材料之間的焊接
激光拼焊技術是指采用先進的激光技術及設備,將一定數量的不同材質、厚 度、涂層的鋼材、鋁合金等材料通過自動拼合和焊接組成一塊整體板材,通過沖 壓制造成為零部件,用以滿足不同的零部件因作用不同而需具有不同材料性能、 厚度及抗腐蝕性等要求。根據零部件的構造及功能需求、材料性質及厚度等要素 的區(qū)別,汽車車身焊接所采用的激光拼焊技術主要包含直線焊接、折線焊接、曲 線焊接、多零件組合焊接等形式,利用激光設備采用拼焊方式將不同性質的材料 焊接成拼焊板,進而沖壓形成最終所需的零部件,這樣的工藝使得現代汽車既輕 便又節(jié)能。
2)液壓成形:可將形狀復雜、要求高精度、空心化的零部件一次整體成形
液壓成形是以液體為傳力介質,在液體壓力和模具型腔的共同作用下,將標 準的管材或板材制成結構復雜的單一整體結構件,用其代替?zhèn)鹘y(tǒng)焊接或鑄造工藝, 既節(jié)省工序又發(fā)揮了材料的最大效能。高強鋼的液壓成形技術可以在保持各項安 全性能指標的同時,實現減重與空間合理利用。液壓成形可分為板料液壓拉深成 形、管材液壓脹形、殼體液壓成形。按照模腔內液體所承受壓力大小差異,還可以 劃分為高壓成形和低壓成形兩種。
3)熱成形:過去十年的技術
熱成形技術是將板材加熱到奧氏體溫度后,然后在模具中進行熱成形,經通 水冷卻,在保持零件良好形狀的前提條件下得到高強度的馬氏體組織。熱成形工 藝能夠很好地解決冷成形過程中存在裂紋、回彈、起皺等缺點,該方法制造的零件滿足汽車輕量化中重量輕、強度高等特點,符合生產及市場需求,在過去十年 中迅速發(fā)展成為汽車制造中的制造工藝技術。
三種汽車工藝輕量化技術具有不同的優(yōu)勢,未來可以根據汽車不同部分零部 件的特點和需求選擇對應的技術。激光拼焊技術的最大優(yōu)點在于可以將不同厚度、 不同材質、不同強度、不同沖壓性能和不同表面處理狀況的板坯拼焊在一起,再 進行沖壓成形。液壓成形技術的最大優(yōu)點在于可以將形狀復雜、要求高精度、空 心化的零部件一次整體成形,適用于汽車領域的沿構件軸線變化的圓形、矩形截 面或各種異形截面空心構件,例如排氣管道、發(fā)動機、副車架主管等部分,具有提 高成形件的強度與剛度、減少模具數量、降低生產成本的優(yōu)勢。熱成形技術適用 于對舒適性、強度和安全性要求高的零件,典型的熱沖壓零件有前、后門左右防 撞桿(梁),前后保險杠橫梁,A/B 柱、地板中通道和車頂加強梁、懸置固定架等 部分,在不降低安全性的同時,達到降低汽車重量的輕量化目的。
4)壓力鑄造:鑄造方法多樣,各有優(yōu)劣
壓力鑄造是一種將液態(tài)或半固態(tài)金屬或合金,或含有增強物相的液態(tài)金屬或 合金,在壓力下以較高的速度填充入壓鑄型的型腔內,并使金屬或合金在壓力下 凝固形成鑄件的鑄造方法。壓力鑄造可分為低壓壓鑄、高壓壓鑄、真空高壓鑄造、 差壓鑄造、擠壓鑄造等。
5)連接技術:輕量化關鍵技術之一,復合連接可使不同連接方式優(yōu)勢互補
連接技術是輕量化制造技術發(fā)展的關鍵技術之一,它關系到被連接結構的性 能、重量、加工工藝、裝配、安全與回收等諸多方面。傳統(tǒng)的連接技術主要有電 阻點焊和情性氣體保護焊接/活性氣體保護焊接(MIG/MAG)。但隨著越來越多的 材料輕量化設計需要,激光焊接、鉚接與自沖鋼接、粘接及復合連接等新的連接 技術逐步發(fā)展并得到越來越多的應用。機械連接技術包括壓焊、鉗鉚、自沖鉚接、 盲鉚和折疊等。采用機械連接技術代替電阻點焊其優(yōu)點在于:可用于多種材料組 合或夾層材料,允許表面帶有涂層,不需加熱(變形小、不改變材料性能),無需 預處理及加工。粘接技術是指利用適宜的膠黏劑作為工藝材料,采用適當的接頭 形式和合理的粘接工藝而達到連接目的。粘接連接產生連續(xù)的連接,應力分布更 加均勻,因而與點焊和機械連接的局部的、斷續(xù)的連接相比,提高了連接剛度。
3. 一體化壓鑄助力整車制造成本下探、效率提升3.1. 一體化壓鑄降本增效,設備成本、模具制造難度、材料要求為主要壁 壘
一體化壓鑄將傳統(tǒng)汽車生產中沖壓和焊裝整合為壓鑄,工藝高度簡化。傳統(tǒng) 汽車生產制造由沖壓、焊裝、涂裝、總裝四大工藝組成。其中,沖壓就是將金屬板 材壓制成車身所需的各個組成部件,而后再采用焊接或鉚接組合的方式制造出大 型鋁制件。而一體化壓鑄則是采用特大噸位壓鑄機,把沖壓與焊裝改為壓鑄,前 兩步合成一步,將多個單獨、分散的零部件高度集成,直接鑄造出大部件。
一體化壓鑄模式與傳統(tǒng)“沖壓+焊接”模式相比,其優(yōu)勢表現在以下幾個方面:
1)生產線、材料、人力三重降本。 ①生產線建設成本及占地面積降低。傳統(tǒng)汽車制造工藝由于需要單獨加工的 零部件眾多,每個零部件均需布置機器和模具,以及生產線周邊的機器臂、傳輸 線、夾具等,全套生產線規(guī)模大、占地多、成本高。相較而言,一體化壓鑄將多 個單獨、分散的零部件高度集成,僅需要 1 大型壓鑄機,少量輔機及模具,省去 了熱處理設備、塑型設備、鈍化設備等,產線建設成本及占地面積大幅下降, 采用大型壓鑄機后,工廠占地面積減少了 30%。 ②材料利用率提升。傳統(tǒng)車身在沖壓過程中原材料不可避免地會產生邊角料, 且其用料復雜,不同零部件通常對應不同種類及材料型號,傳統(tǒng)沖壓-焊接工藝, 通常板材利用率僅為 60%-70%。然而一體化壓鑄是將液體金屬一比一等同于鑄件 用料,材料利用率更高。此外由于僅使用單一鋁合金,車身回收后可直接融化重 制,回收利用率在 90%以上。 ③人力成本降低。傳統(tǒng)車身制造涉及焊接工序,焊接點眾多,需要大量的焊 接技術工人,目前國內主流焊裝工廠通常配備 200-300 個工人。采用一體壓鑄技 術后,由于焊接點減少,所需的技術工人至少可縮減到 30-40 人。
2)工藝流程簡化,生產效率提升。 傳統(tǒng)車身的制造工藝主要分為沖壓-焊裝-涂裝-總裝四大環(huán)節(jié)。主車廠采購由 全國各供應商通過沖壓、壓鑄制造的多個結構件,將之組裝連接(包括焊接、鉚 接、涂膠等)在一起,形成汽車的白車身總成。而一體化壓鑄工序中沖焊與熱處理 工作量減少、省去大量涂膠工藝環(huán)節(jié),生產效率得到大幅提升。特斯拉 Model Y 后地板采用一體式壓鑄工藝,所有零件一次壓鑄成型,應用了新合金材料,一體 壓鑄的后地板總成不再熱處理,制造時間由傳統(tǒng)工藝的1h-2h縮減至3min-5min。
3)車身重量減輕,減少電池裝機量。 根據車乾信息,電池降本是鋼換鋁式車身材料增加成本的 6.6 倍。特斯拉新 一代一體壓鑄底盤有望降低 10%車重,對應續(xù)航里程增加 14%。以普通電動車電 池容量 80kwh 為例,若采用一體壓鑄車身減重并保持續(xù)航里程不變,則電池容量 可減少約 10kwh。按照磷酸鐵鋰電池 pack 成本 800 元/kwh 計算,則可降低成本 8000 元。
除上述優(yōu)勢外,一體化壓鑄同樣具有一定劣勢或是進入壁壘,具體而言:
1)設備投入成本高。一體化壓鑄件的投影面積更大,壓鑄機需要更大的鎖模 力防止模具脫落,目前市場上最大規(guī)格的壓鑄機為 12000T。隨著鎖模力提升,一 臺重型壓鑄機的采購價往往要上億,而傳統(tǒng)沖壓機僅需千萬元。
2)模具制造難度提升。模具是決定零部件的精密程度,支撐零部件強度的關 鍵。壓鑄模具較為復雜,加工成本高,隨著壓鑄機鎖模力不斷提升,對模具抗壓 力、形狀設計要求提升明顯,模具的設計難點在于需要考慮熱平衡、脫模、進漿料 方向等等諸多問題。此外模具原材料的選取與創(chuàng)新也至關重要,材料端需要較高 的高熱穩(wěn)定性、高溫強度、耐磨性、韌性、導熱性等性能。
3)原材料需要免熱處理高強韌鋁合金。一體化壓鑄零件通常具有尺寸大、壁 厚薄、結構復雜等特點,這就對鋁合金材料性能提出了更高的要求。綜合考慮使 用性能、工藝特點和生產條件等因素,一體化壓鑄鋁合金材料不僅在常規(guī)性能上 比普通壓鑄高,而且還有其獨特的要求。包括高韌性、優(yōu)異的鑄造性能、高的連接 包容性、更高的微量元素和雜質元素的容忍度以及長效高效的變質劑。
4)工藝復雜,對參數經驗要求高。一體化壓鑄工藝復雜,全工藝要素均有較 高要求。壓鑄工藝對生產合格的汽車結構件十分重要,正確地選擇壓射模式、壓 射參數等有利于減少壓鑄件中的缺陷。壓鑄冷卻水的布局、周邊機的設置、采用 的壓力參數等是通過多年項目的經驗積累下來的,因此如果要保證較高的產品良 率,需要多年壓鑄參數經驗的累積。
3.2.上游:材料端競爭充分,模具端未上市企業(yè)為主,設備端力勁科技位居龍頭
1)材料:一體化壓鑄需要免熱處理鋁合金材料
熱處理易致大尺寸壓鑄件形變,免熱處理材料成為重要技術壁壘。熱處理是 保障壓鑄零部件機械性能的有效途徑,但也易引起汽車零部件尺寸變形及表面缺 陷。一體化壓鑄的大型鋁合金部件對精度要求較高,熱處理過程易引起汽車零部 件尺寸變形及表面缺陷,雖然通過矯正工藝可以改善一定的尺寸精度,但會降低 良品率,導致成本急劇上升,因此免熱處理鋁合金材料是大型一體化壓鑄結構件 的關鍵。國外免熱處理鋁合金材料廠商主要有美國鋁業(yè)、德國萊茵菲爾德和特斯 拉,國內廠商正在積極研發(fā),目前立中集團、上海交大、廣東鴻圖、湖北新金洋已 研制成功。
2)模具:6000 噸模具已量產,12000 噸正在研發(fā)中
一體化壓鑄對模具的強度及韌性要求更高。與其他鑄造工藝相比,壓鑄工藝 特性主要體現在“高速充型與高壓凝固”上,在溫度、真空、成型方案、工藝參 數、后處理等方面都比傳統(tǒng)鑄造工藝存在更高要求。相比普通壓鑄的模具,一體 化壓鑄模具更復雜,對強度和韌性要求更高。一般壓鑄廠商不具備大型壓鑄模具 的設計能力,通過外部采購來滿足需求,目前我國的大型壓鑄模具廠商主要有廣 州型腔、寧波臻至、寧波賽維達、合力科技等。
3)壓鑄機:力勁科技為行業(yè)龍頭,12000 噸以上壓鑄機有望助力整車級別一 體化壓鑄件
大型壓鑄機是汽車實現一體化壓鑄的基礎。根據佐思汽研,一般來說一體化 壓鑄所需要的壓鑄機鎖模力都在 6000T 以上,當前全球能生產 6000T 壓鑄機的 企業(yè)有海外的意德拉集團(力勁科技全資子公司)和瑞士布朗集團,國內的力勁 科技、海天金屬和伊之密,其中力勁科技為國內龍頭。更大噸位的壓鑄機意味著壓鑄件的尺寸和結構可以進一步突破,目前特斯拉、力勁科技、廣東鴻圖、海天金 屬等企業(yè)均在研發(fā) 12000 噸以上的壓鑄機。2022 年 9 月,力勁科技與廣東鴻圖 發(fā)布 12000 噸超大型智能壓鑄單元,這是迄今為止全球最大噸位的壓鑄機,有望 助力整車級別一體化壓鑄件。
3.2.2. 中游:文燦、鴻圖等布局企業(yè)數量多,壓鑄制造行業(yè)集中度較低
目前國內壓鑄行業(yè)集中度較低,參與企業(yè)眾多。根據文燦股份招股說明書, 截至 2016 年國內注冊壓鑄相關企業(yè)超 12600 家,企業(yè)主要分布在廣東、江蘇、 浙江、重慶、山東等地,生產規(guī)模較大、專業(yè)化程度較高的企業(yè)主要集中在珠三角 和長三角地區(qū)。國內自主品牌的汽車壓鑄供應商可分為兩大類,一類是下游主機 廠配套壓鑄事業(yè)部或壓鑄子公司,為主機廠提供壓鑄件產品配套,如長城汽車的 壓鑄事業(yè)部、比亞迪的弗迪精工、一汽集團旗下的一汽鑄造等。另一類是第三方 汽車壓鑄件供應商,其中僅少數企業(yè)具備生產中大型壓鑄產品能力。
3.3. 特斯拉引領輕量化發(fā)展,大眾、新勢力等紛紛跟進3.3.1. 特斯拉:率先推出一體化壓鑄,引領行業(yè)發(fā)展方向特斯拉率先推出一體化壓鑄后車身,Model Y 的后車身實現減重提效。2020 年 4 月 30 日,特斯拉在一季度財報文件中首次披露了 Model Y 的一體壓鑄后車 身。和 Model 3 相比,這塊區(qū)域實現了將 70 個零件精簡為 1 個零件的進步。將 Model 3 后車身 70 個零件合而為一之后,Model Y 的后車身制造時間大大縮短, 是 Model 3 的幾分之一。此外,盡管 Model Y 相比 Model 3 尺寸全面增大,但Model Y 的一體壓鑄后車身僅重 66 公斤,反而比尺寸更小的 Model 3 同樣部位輕 了 10-20 公斤。
后底板成功減重后,Model Y 實現一體式壓鑄后底板總成。根據汽車工藝師 公眾號,2020 年 9 月特斯拉宣布 Model Y 將采用一體式壓鑄后地板總成,原來通 過零部件沖壓、焊接組裝的后地板總成將采用一體式壓鑄一次成型,相比原來形 式可減少 79 個部件,焊點由 700-800 個減少到 50 個,同時由于應用了新型鋁合 金材料,特斯拉一體壓鑄的后地板總成不需要進行熱處理,整個制造時間由傳統(tǒng) 工藝的 1-2h 縮減至 3-5min,并且能夠在廠內直接供貨,整體制造成本下降 40%。 同時,特斯拉宣布下一步計劃將應用 2-3 個大型壓鑄件替換由 370 個零件組成的 整個下車體總成,質量將進一步降低 10%,對應續(xù)航里程可增加 14%。此外,特 斯拉已經申請采用巨型壓鑄設備一次壓鑄整個白車身的技術。
前身車和 Cybertruck 一體化壓鑄接力后底板總成。Model Y 后底板總成采 用的是 6000 噸壓鑄機,而要實現前身車和 Cybertruck 一體化壓鑄需要更大鎖模 力的壓鑄機。2020 年 3 月特斯拉在財報會上宣布已經訂購 8000 噸壓鑄機用來生 產 Cybertruck 車身后底板。Cybertruck 采用一體成形金屬無烤漆框架將鐵、鋁、 硅和鎂等金屬塊送進爐內,以攝氏 850 度高溫熔化后,通過多道的氣體、碳化硅 等物質加工,將液態(tài)金屬灌入模具,高壓成形后以機械手臂取出,再通過 X 光和 激光檢驗加工,完成整個工序。 根據電動新視界,Giga Press 壓鑄機和鋁合金配方為特斯拉一體化壓鑄的壁 壘。特斯拉的一體化壓鑄機 Giga Press,由特斯拉和壓鑄機廠商 IDRA Group 聯 合定制,深度參與了軟硬件的設計制造,其大小與房子相當,長 19.5 米、高 5.3 米,重達 410 噸。除了壓鑄機定制設計與開發(fā)的技術壁壘之外,如果沒有大批量 生產帶來的規(guī)模效益,車企很難分攤壓鑄工藝使用的昂貴的壓鑄機和壓鑄模具的 綜合成本。Giga Press 所使用的鋁合金材料是特斯拉為改進生產工藝的獨家配方, 是一種不需要涂層和熱處理的高強度合金。由前蘋果合金專家查爾斯·柯伊曼主 導研發(fā),柯伊曼 2016 年加入特斯拉,同時領導特斯拉和 Space X 的材料工程團 隊。
CTC 技術配合一體化壓鑄技術,開辟新方向。在 2020 年 9 月的電池日上, 特斯拉發(fā)布了全新的整包封裝技術 CTC(Cell to Chassis),即取消 Pack 設計, 直接將電芯或模組安裝在車身上。CTC 技術有助于將車輛的結構平臺進一步單元 化,從而進一步降低制造成本。馬斯克曾表示,采用了 CTC 技術后,配合一體化 壓鑄技術,可以節(jié)省 370 個零部件,為車身減重 10%,將每千瓦時的電池成本降 低 7%。除特斯拉,寧德時代計劃在 2025 年實現集成化 CTC,2030 年實現智能 化 CTC。根據寧德時代董事長曾毓群介紹,寧德時代的集成化 CTC 技術不僅會 重新布置電池,還會納入包括電機、電控、DC/DC、OBC 等動力部件。
3.3.2. 大眾:全新 SSP 平臺將引入一體化壓鑄,后車身一體式鋁壓鑄樣件成功下線大眾汽車 MLB-evo 平臺混合車身結構材料輕量化,采用 52%高強度鋼材和 48%鋁合金材料,減重同時整車性能提升。占比 13%的熱成型鋼被用于需要極高 強度的 A、B 柱等關鍵位置,1400mPA 抗拉強度保證駕駛艙在受到碰撞后依然為 駕乘者提供周全保護;使用比例達 39%的冷成型鋼則被用于前圍板、前后翼子板 等部位,防止在駕駛艙被擠壓時發(fā)生車門無法打開的情況。發(fā)動機艙蓋板、前后 車門板及側圍板等部位的鋁制板材占車身選材的 30%,在保證輕量化的同時,還 與采用擠壓鋁型材的防撞梁、吸能盒等一同吸收和弱化碰撞時激發(fā)的能量。此外, 15%鋁鑄件材料加持于前后避震器支座等部件也令整車性能得到進一步提升。
全新一代途銳是首款使用混合式車身結構的 SUV,實現減重 106 公斤。MLB Evo 平臺采用了縱置發(fā)動機布局,使得車身前后配重更加平衡,同時動力配置自 由度也更高。更合理的布局和輕量化設計,不僅能夠提升車輛舒適性,也能提升 駕控體驗。大眾官網顯示,作為誕生于 MLB Evo 平臺的杰出之作,全新一代途銳 是首款使用混合式車身結構的大眾汽車品牌 SUV 車型。其不僅將混合式車身結構 的眾多優(yōu)點集于一身,而且縱置發(fā)動機架構也能大幅提升車輛的基準設計性能。 根據大眾官網數據,上述技術的運用讓全新一代途銳在重量減輕 106 公斤的同時, 安全性也有所保障,取得了歐盟新車安全評鑒協(xié)會碰撞測試五星安全認證。
4 種輕量化材料+14 種車身連接工藝,奧迪 A8 全新推出。
1)材料:根據 AI 汽車制造業(yè)數據,新一代奧迪 A8 車身材料除了鋁合金、高 強度合金鋼、鎂合金外,首次應用了碳纖維復合材料,占比分別為 58%、40.5%、 0.5%、1%。車身的整體框架由鋁型材搭建,關鍵部位采用鋁制鑄件進行聯接,保 證結構強度,車身表面采用鋁制鈑金件。碳纖維復合材料的應用使得后座背板密 度減少 45%,重量減輕 50%。四種材料如果按照種類再進行細分的話,材料種類 可以達到 29 種,其中包括 11 種鋼材、16 種鋁材、1 種鎂材和 1 種碳纖維復合材 質。
2)連接工藝:多種材質的應用意味著車身連接方式需要進行改進和優(yōu)化,尤 其是碳纖維材質的加入對車身連接技術提出了更高的要求。基于跑車奧迪 R8 的 經驗,新一代奧迪 A8 車身的連接方式達到了 14 種,其中包括 MIG 焊、遠程激光 焊等 8 種熱連接技術和沖鉚連接、卷邊連接等 6 種冷連接技術。
大眾推出下一代 SSP 平臺,計劃開始應一體化壓鑄。根據智電汽車,SSP 平 臺是一個集純電動、全面互聯和高度可擴展性于一身的全新汽車平臺,這套平臺 將在 2024 年正式啟動,SSP 平臺是在 MQB、MSB、MLB 等三個燃油車平臺, 和 MEB、PPE 兩個純電動汽車平臺基礎上,整合成一個全新的可擴展系統(tǒng)平臺, 適用于集團旗下所有品牌和所有級別車型的機電一體化平臺架構。SSP 平臺將電 池、軟件、車身、自動駕駛等方面進行整合,生產更加簡潔,效率更高。而 SSP 平臺最大的亮點就是完美實現四電機布局,可以達成前輪/后輪/全輪驅動模式。大 眾計劃于 SSP 平臺開始應用一體壓鑄,車身一體式鋁壓鑄件樣件已成功下線。
3.3.3. 新勢力奮起直追,傳統(tǒng)車企紛紛跟進國內新勢力車企積極布局“一體化壓鑄”,蔚來、小鵬、理想等奮起直追。除造車新勢力外,長安、東風、長城等傳統(tǒng)車企也開始布局汽車一體化壓鑄 領域。2023 年長安汽車首個一體化前機艙鑄件于 1 月 15 日晚成功產出,標志著 長安汽車躋身成為國內掌握超大型一體化結構件研制及生產調試技術的企業(yè),一 體化車身項目正式邁入實體鑄件階段。此外,東風汽車也在布局一體化壓鑄,上 海交大中標其車身結構件材料項目。長城推出了全球化高智能模塊化技術平臺— —檸檬平臺,該平臺從設計、材料、結構、工藝全過程確保輕量化性能打造;使用 高強鋼超過 70%,通過使用“一體式”熱沖壓成形門環(huán)和“不等厚”鋼板(TRB) 的應用,降低零部件厚度,減少零搭接邊,減輕重量,在保障了車身強度的同時減 輕了車體重量。
聯興
相關新聞
當前汽車各式各樣,發(fā)動機、變速箱原理五花八門,不過好多技術都是幾十年前的老技術,汽車制造商現在對發(fā)動機、變速箱的改良效果微乎其微,動力總成這方面是不是已經無法發(fā)展了?30年前的發(fā)動機和現在的發(fā)動機是不是沒什么多大區(qū)別?
汽車覆蓋件具有尺寸大、相對厚度小、形狀復雜等特點,決定了在沖壓成形中板料變形的復雜性,變形規(guī)律不易被掌握,不能定量地對主要工藝參數和模具參數進行計算,在工程實踐中還主要運用經驗類比來進行沖壓工藝設計。
以維修、保養(yǎng)為主的后市場產業(yè)是汽車價值鏈的終端,也是重要的民生服務業(yè)。近年來,隨著消費市場逐漸復蘇和中國汽車產業(yè)的不斷升級,這一產業(yè)也迎來了新的機遇和挑戰(zhàn)。
機動車成為重要大氣污染源,碳減排目標下汽車低碳化發(fā)展刻不容緩。根據 中國政府網發(fā)布的《第二次全國污染源普查公報》,2017 年全國大氣氮氧化物排 放量 1785.22 萬噸,顆粒物排放量 1684.05 萬噸,揮發(fā)性有機物排放量 1017.45 萬噸。
直面挑戰(zhàn),把握機遇,2024中國汽車供應鏈大會在武漢啟幕
隨著電動化、智能化和網聯化的技術變革浪潮席卷全球,汽車產業(yè)鏈供應鏈迎來了新機遇、新挑戰(zhàn)。2024年9月24日-26日,由中國汽車工業(yè)協(xié)會和東風汽車集團有限公司聯合主辦的“2024中國汽車供應鏈大會暨第三屆中國智能網聯新能源汽車生態(tài)大會”在武漢市舉辦。本屆大會以“新挑戰(zhàn)、新對策、新機遇——推動中國汽車供應鏈可持續(xù)發(fā)展”為主題,共設置1場閉門會議、1場大會論壇和4場主題論壇等6場會議,并同期舉行汽車供應鏈發(fā)展報告發(fā)布、創(chuàng)新成果推介、國際汽車及供應鏈(香港)高峰論壇&2025香港車博會發(fā)布及啟動儀式、中國汽車供應鏈協(xié)同創(chuàng)新全國行——首站(東風汽車站)等一系列發(fā)布或配套活動。
慧聰汽車配件網】4月21-23日,箭冠汽配遼寧省加盟商代表大會在遼寧·沈陽沈遼路金際酒店盛大召開,箭冠汽配總部、分公司領導以及遼寧省加盟商代表出席了本次會議,現場座無虛席。
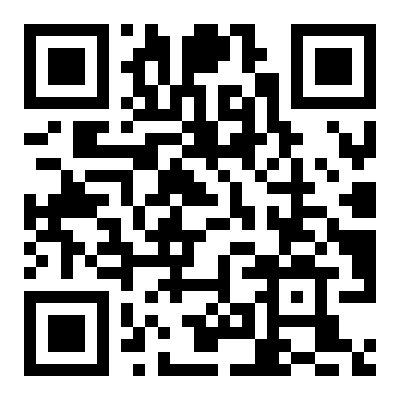
移動端二維碼
儀征市聯興汽車配件制造有限公司
Copyright © 2024 儀征市聯興汽車配件制造有限公司 | 營業(yè)執(zhí)照